Any topic (writer's choice)
Instructions
Inventory and Supply Chain Design ProblemsAfter reading Chapters 9 and 12 in Operations Management: Processes and Supply Chains and the article by Mageto, Prinsloo, and Rose, solve the problems posed in Question 5 from page 370 in Chapter 9 and Question 9 on page 504 in Chapter 12 and post your answers. Discuss how to assist the SME firms make better outsourcing decisions in the article.Please provide references
Answer
5.Order quantityPrice per unit1-999$7.501000-4999`$7.255000 or more$6.5Annual demand50 weeks * 350 baseballs = 17500noteHolding cost = 38% of the total purchasing price = 0.38* price per unitordering cost = 100 dollarsEconomic order quantity= ((2* total demand* ordering cost)/ holding cost)Economic order quantity for 1-999= (2*17500*100)/0.38*7.5) = 1108Economic order quantity for 1000-4999`=(2*17500*100)/0.38*7.25)=1127Economic order quantity for 5000+= (2*17500*100)/0.38*6.5)=1190How many baseballs should the team be buying per orderSo answer is 1000-4999Total annual cost associated with best order quantity.Total cost is calculated by taking into cumulation the holding cost + ordering cost plus the material cost.Materials cost= 17500* 7.25 = 126 875Ordering cost = (total quantity/Economi...
To avoid plagiarism, part of the answer is hidden. Click on the button below to order the full answer.
Order Answer
Back
Price Calculator
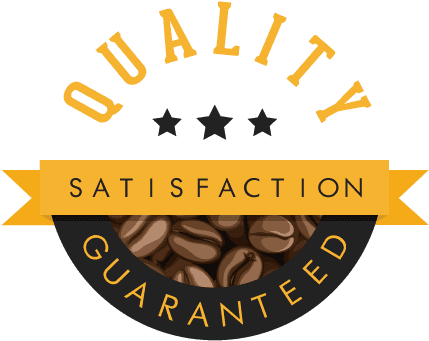
Why we are Ranked the best
- Unlimited Revisions
- Free 24/7 Support and chat
- Money back guaranteed
- Low prices with discounts
- Experienced writers.
- Free Unlimited support